汽車線束是汽車電路的網(wǎng)絡(luò)主體,沒有線束也就不存在汽車電路。隨著人們對汽車的安全性、舒適性、經(jīng)濟性和排放性要求的提高,汽車上的電器配置、功能也越來越多,所以連接各個電器件的線束也越來越復雜,成為當代汽車故障的多發(fā)環(huán)節(jié),也因此在汽車設(shè)計和生產(chǎn)制造中受到越來越多的關(guān)注。如何提高汽車線束的綜合性能成為關(guān)注的焦點。在汽車線束的整體設(shè)計中,三維布局是前提。本文將重點闡述這部分。
1汽車線束設(shè)計流程
汽車線束的設(shè)計流程見圖1,詳細分析如下。
1)由主機廠電氣工程師提供整車電氣系統(tǒng)的功能,電氣負荷及相關(guān)的特殊要求,電器件的狀態(tài)、安裝位置,線束與電器件對接的形式。

圖1 汽車線束設(shè)計和制造流程
2)根據(jù)電氣原理圖對每個電氣子系統(tǒng)及回路進行電源分配,其中包括搭鐵點的分配。并繪制相應的整車電氣原理圖。
3)繪制三維線束布置圖。
4)根據(jù)各子系統(tǒng)電器件的分布情況,確定線束的布線形式及在汽車上的走向;確定線束的外保護形式及過孔的保護;并根據(jù)電器件本身的插接件確定線束上與其對接的端子和護套的型號:繪制二維線束圖。
5)根據(jù)凍結(jié)的三維線束布置圖和原理圖,校核二維線束圖;確認無誤后方可發(fā)圖,經(jīng)認可后試制、生產(chǎn)。
2線束三維布局走向設(shè)計
線束的走向布局及分段,是根據(jù)車身鈑金的具體情況,結(jié)合全車電器件的分布綜合來考慮的。線束的走向分段不可拘泥某種形式,而是要在車身鈑金能夠滿足線束布置的前提下,從整車電氣角度來考慮其分布走向。
1.線束三維布局走向的主要原則
下面詳細介紹線束三維布局走向中需要考慮的主要原則。
1)裝配工藝性好
線束的走向分段設(shè)計一定要滿足易于裝配這個前提,盡量不要給總裝增加過多的工序,可考慮分裝,如門線、儀表板線等:同時,要考慮最好不要使用特殊工具就可以完成裝配。
2)可維護性好
這一點是與第l點相呼應的,不僅僅要易于裝配,在售后維修方面,也要易于拆卸,不可以因為要維修某個電器件需要拆下某段線束,而拆除其他多個零部件,否則就將增加不必要的維修工時。
基于這一點,在線束設(shè)計時需要考慮如下幾點:
①所有線束的插接件應該布置在手可以觸及的地方?;蚝唵尾鹦兑恍┝悴考?。可以觸及插接件;
②對于只能用一只手插拔的插接件,另一端插接件應該固定在車身上;
③同一部位的插接件應該應用顏色、大小、內(nèi)部定位等方法,防止錯裝;
④插接件末端的線束應該預留一定的長度,以便于插接件的插拔,對于開關(guān)端的線束建議預留80~100mm,儀表、音響、空調(diào)面板等維修率比較高的電器件。其后端線束預留到可以容易插拔的長度;
⑤熔斷絲盒的線束要留有足夠的余量,以便于熔斷絲盒的拆卸。
3)回路盡可能地短
在拆裝工藝都考慮后,需要考慮如何布線能使電線回路盡可能的短,因為回路短有如下好處:①電線上面的壓降小,電器件獲得的電壓高或者得到的信號衰減?。孩诳梢詼p輕整車質(zhì)量;③可以降低線束成本。
4)盡可能地減少線束分段
這一點有的時候和裝配工藝性是矛盾的,因為有的時候為了方便安裝便要將原本可以是1條的線束分成2段.這是需要在實際線束三維設(shè)計中權(quán)衡的。因為增加線束分段,勢必要增加線束間的對接插接件。而增加對接件則需要考量以下幾點:①增加了線束上面的電壓降,或是增大了信號的衰減;②增加了電氣連接的潛在的不可靠點;③需要增加安裝點或安裝支架,以固定對接件;④增加線束組裝工時和物料成本。
所以我們經(jīng)常會在一些德系車輛上看到貫穿發(fā)動機艙、乘客艙、行李艙的一根大線。這就是少分段的典型設(shè)計。
5)要考慮電磁兼容與抗電磁干擾這方面。
不僅僅是要從線材的選擇上來做(如采用雙絞線、屏蔽線等),更要從線束的布線走向上來考慮。如某些歐系的蓄電池后置行李廂的車型,因為要將電流傳輸給發(fā)動機艙電氣盒及起動機,所以會有一根縱貫全車的大線徑導線,時刻通以較強電流。這個時候,如果還是按照傳統(tǒng)布線,將此大電流導線與其他信號線不加以區(qū)別一并放在同一束線中,勢必會對信號線產(chǎn)生干擾,所以通常會將此大電流導線單獨布置走向,并與普通線束留出足夠遠的距離,同時要求鈑金做出一條凹槽以盛放導線,并可起到一定電磁屏蔽作用。雖然如此處理會增加成本。可是這成本是必要的。
2.線束布置時需要注意的其他細節(jié)
除上述5點基本原則之外,在線束的布置時還有如下的細節(jié)需要注意,以保證線束布置的可靠性。
1)在線束最大的裝配公差條件下,所有布置在運動件附近的線束,應該和運動件之間保留足夠的距離,此距離由運動件的運動量來決定。
2)在線束最大的裝配公差條件下,線束與相對靜止的部件之間需要保留最少為6mm的間隙,除非線束已經(jīng)被固定在這個部件上。
3)線束分支必須有足夠的松弛,以使線束不會與其連接的器件增加應力。我們應在線束的3D數(shù)模上將此松弛度表現(xiàn)出來,以使3D狀態(tài)更加接近于實際狀態(tài)。
4)為了阻止搭鐵片破壞主干上的任何線束,裝車時線束主干上的搭鐵片到線束主干上的任何線束最小間隙應維持在25mm以上。
5)通常情況下,距離線束插接件120mm處需要增設(shè)固定點,目的是盡可能減少插接件內(nèi)的端子所承受線束震動和質(zhì)量所帶來的負擔。
6)從發(fā)動機本體往車身上布置的線束分支,要盡量布置在比較開闊的地方,且要留出足夠的長度余量.以防止發(fā)動機運轉(zhuǎn)過程中給線束造成磨損或拉應力損傷。
7)線束布置時應避開燃油管路,線束上兩固定點之間的長度應小于300mm。另外,拐角處需要增設(shè)固定點。
3.搭鐵策略
搭鐵點的分配在汽車線束設(shè)計中尤為重要,因為它是保證信號傳遞的完整性的重要組成部分,如果搭鐵點選擇不當,就易造成信號干擾,從而影響某些電器正常功能的實現(xiàn)。因此在汽車線束的設(shè)計過程中,一定要根據(jù)用電設(shè)備的性質(zhì)、功能的不同,對搭鐵線和搭鐵點作合理的分配,才能最大限度地保證汽車上各電氣設(shè)備的良好工作狀態(tài)。
按照搭鐵回路的功能來劃分。將電氣設(shè)備分為2類。一類為重要件,一類為普通件。其中重要件包括發(fā)動機控制單元(ECU)、制動防抱死系統(tǒng)控制單元(ABS)及安全氣囊系統(tǒng)控制單元(SRS)及其它涉及整車安全的控制單元。該類電負荷不僅對于整車性能及安全至關(guān)重要,而且該類電氣設(shè)備屬敏感設(shè)備,易受其它用電設(shè)備干擾。
因此,重要件的搭鐵點必須單設(shè),而不能和其它電氣設(shè)備共用搭鐵點.以免受其它電器件的干擾,對汽車的性雒:及安全性造成影響。但在有些車輛的設(shè)計中,為提高其搭鐵可靠性.會對某些重要電器件進行復式搭鐵,如安全氣囊。這樣做的目的是如果其中一處搭鐵失效.系統(tǒng)可以通過另一搭鐵點搭鐵,以確保系統(tǒng)安全工作,同時還可以降低接地阻抗。此外,EMC/RFI搭鐵也需要單獨設(shè)立搭鐵點(如音響),目的是保證收音狀態(tài)的電磁兼容通過性。
至于普通件,該類設(shè)備對于整車而言。重要性并不是很大。一般為增進駕乘人員的舒適性而加設(shè)的電氣設(shè)備。因此,對于該類器件可以根據(jù)情況相互組合,共同鉚接搭鐵。還有一點需要提醒的是:一定要保證全車搭鐵點與蓄電池負極可靠連接。此外,防靜電搭鐵的相關(guān)內(nèi)容可參考文獻。
圖2是典型的轎車的搭鐵分配方式。圖2中搭鐵點的搭鐵位置參見表1。
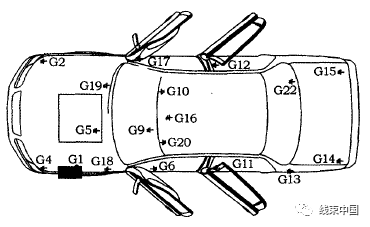
圖2 典型轎車的搭鐵分配方式
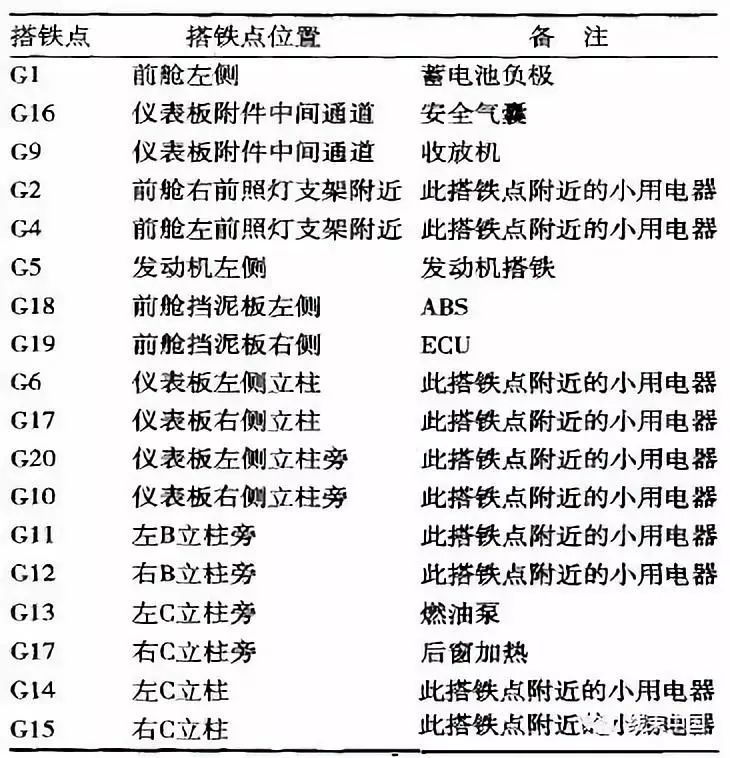
表1 圖2中搭鐵點的搭鐵位置
4.結(jié)束語
以上是線束開發(fā)過程中3D設(shè)計的一些基本原則,需要在實際設(shè)計中靈活運用;待在設(shè)計完畢做出樣品后,需要用一系列的測試來驗證(包括試驗室的測試和實車道路測試等),以確保設(shè)計的可靠性。