汽車(chē)覆蓋件及其模具零件型面面積大、造型特征復(fù)雜,嚴(yán)重制約模具鉗工的研合效率,而模具研合精度直接影響制件的表面成形質(zhì)量。交付模具周期與覆蓋件表面質(zhì)量已成為主機(jī)廠衡量模具企業(yè)技術(shù)水平的兩大重要指標(biāo)。
隨著時(shí)代的發(fā)展與科學(xué)技術(shù)的進(jìn)步,越來(lái)越多的計(jì)算機(jī)模擬輔助軟件被應(yīng)用到模具制造及加工中。通過(guò)AutoForm軟件模擬成形過(guò)程,分析板料在成形過(guò)程中各個(gè)區(qū)域的變薄情況,根據(jù)不同區(qū)域變薄量來(lái)補(bǔ)償模具零件各區(qū)域的偏差間隙,取代傳統(tǒng)依靠鉗工研合經(jīng)驗(yàn)來(lái)補(bǔ)償模具零件型面間隙,更加精準(zhǔn)地完成模具零件型面各區(qū)域的間隙偏差補(bǔ)償,實(shí)現(xiàn)在合模過(guò)程中模具閉合時(shí)模具型面與制件完全貼合,減少了鉗工手工修改模具零件型面的工作量,提升了模具研合效率,實(shí)現(xiàn)效率與制件成形質(zhì)量的雙重保證。
汽車(chē)模具研合現(xiàn)狀
1
模具零件型面的研合精度直接影響外覆蓋件的表面成形質(zhì)量及尺寸精度,故主機(jī)廠對(duì)模具驗(yàn)收的研合要求也是模具移交的重要指標(biāo)之一,合資及國(guó)產(chǎn)品牌主機(jī)廠對(duì)重要的模具零件型面要求研合率均要大于95%。
行業(yè)的高標(biāo)準(zhǔn)、高要求促使模具制造企業(yè)不得不投入更大的人力、物力和財(cái)力去提升企業(yè)的技術(shù)水平,縮短模具的研合工時(shí),減少模具制造成本是提高企業(yè)在模具行業(yè)中競(jìng)爭(zhēng)力的重要途徑。
表1 覆蓋件拉深工序研合標(biāo)桿工時(shí)
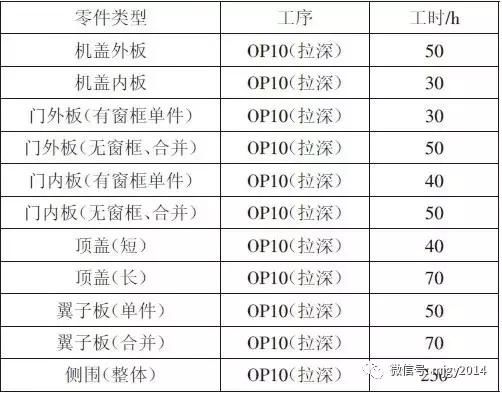
某中日合資模具制造企業(yè)給出的各類(lèi)型車(chē)身覆蓋件研合所需的標(biāo)桿工時(shí)如表1所示,單工序拉深研合工時(shí)長(zhǎng),有較大的提升空間。
影響研合工時(shí)原因分析
2
影響模具零件型面的研合工時(shí)因素有:
01
模具零件材質(zhì),不同的材料在長(zhǎng)時(shí)間的放置后會(huì)發(fā)生去應(yīng)力變形,變形量不一致。
02
數(shù)控機(jī)床的加工精度,高精度的機(jī)床能減小模具零件型面的加工偏差。
03
制件結(jié)構(gòu),側(cè)圍等大型覆蓋件的研合工時(shí)會(huì)大于機(jī)蓋等。
04
模具在壓力機(jī)上的受力變形,不同壓力機(jī)的壓力不同,引起的模具零件變形量有較大差異。
05
制件型面的角度差,由于特征造型需要,不同區(qū)域與沖壓方向形成不同的角度,多角度的存在也增加了研合難度。
06
板料在拉深過(guò)程中的變薄,制件各區(qū)域的料厚均小于原始厚度且料厚不均等,直接導(dǎo)致模具閉合瞬間板料和模具零件型面不能同時(shí)接觸,局部區(qū)域出現(xiàn)離空現(xiàn)象。
提升模具研合效率的常規(guī)對(duì)策
3
針對(duì)模具零件材質(zhì)產(chǎn)生的去應(yīng)力變形而導(dǎo)致模具零件型面研合困難,主機(jī)廠和模具制造生產(chǎn)商對(duì)模具各部件材質(zhì)的選用已有自己的參考標(biāo)準(zhǔn),如表2所示。
表2 模具材質(zhì)
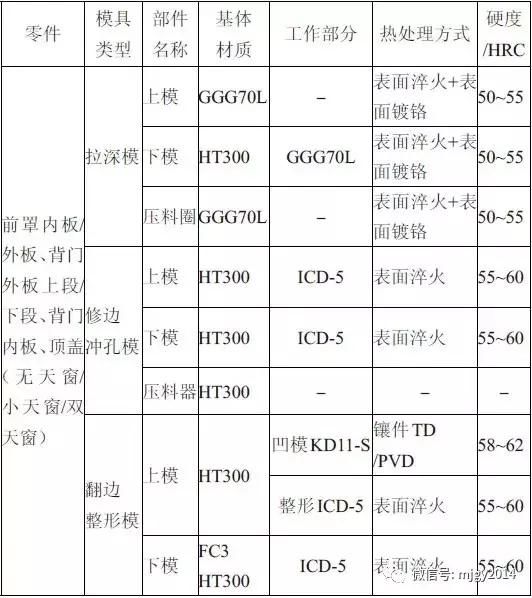
針對(duì)模具在壓力機(jī)上的受力變形而導(dǎo)致模具零件型面產(chǎn)生間隙偏差,許多企業(yè)已重視并有了相應(yīng)的改善措施,通過(guò)Jstamp和AutoForm軟件分析模具在壓力機(jī)上的受力變形,將模具零件型面各區(qū)域的變形量用階梯線與數(shù)值直觀地展示,如圖1和圖2所示。
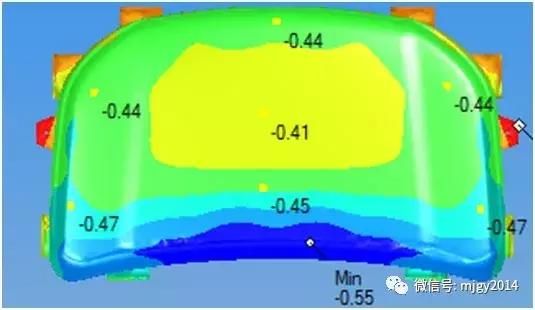
圖1 Jstamp計(jì)算凸模變形量
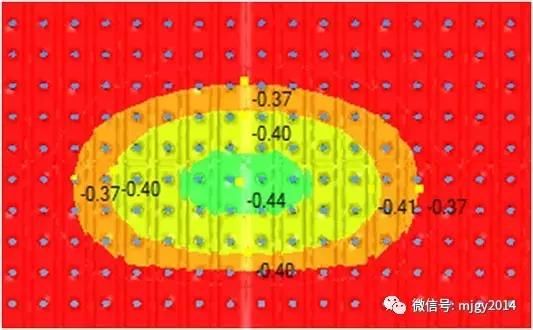
圖2 Jstamp計(jì)算模具變形量
通過(guò)提取模具零件變形階梯邊界線與變形量,采用UG或CATIA軟件將變形量補(bǔ)償?shù)郊庸?shù)模,消除因模具受力變形而導(dǎo)致的模具零件型面高度差,提升鉗工的研合效率,減少鉗工的研合工時(shí)。
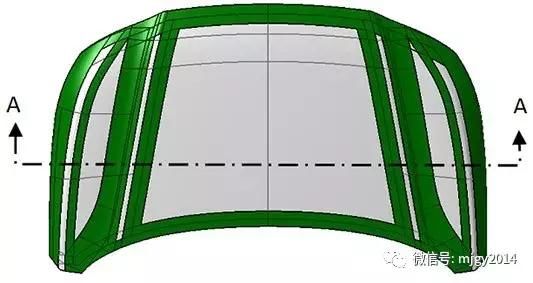
圖3 機(jī)蓋研合要求
針對(duì)制件型面角度差導(dǎo)致的研合難度,以某機(jī)蓋外板為例,黑色部位為要求有研合的型面,灰色部位無(wú)研合要求,如圖3所示。由于側(cè)壁面及凹成形區(qū)域的存在,截面上各區(qū)域零件型面的切向角度與沖壓方向均存在不同的角度差,如圖4所示。
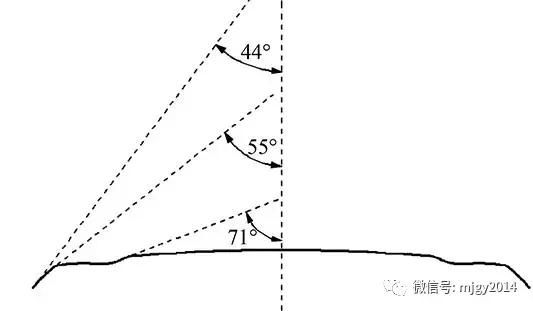
圖4 橫截面角度差(圖3A-A)
制件型面角度差的存在導(dǎo)致在上、下模合模過(guò)程中不同角度區(qū)域型面間隙存在差異,如圖5所示,上模到底前20mm時(shí),側(cè)壁的型面間隙為15.61mm,常規(guī)的工藝會(huì)結(jié)合以往研合經(jīng)驗(yàn),根據(jù)不同的區(qū)域進(jìn)行相應(yīng)的強(qiáng)壓(零件型面偏差加工)處理(見(jiàn)圖6),以減小或消除角度差導(dǎo)致的型面偏差,確保上、下模各區(qū)域型面同時(shí)接觸板料。
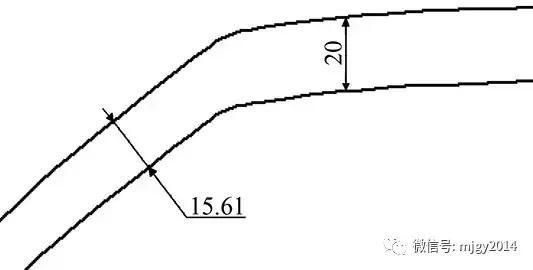
圖5上模到底前20mm型面間隙
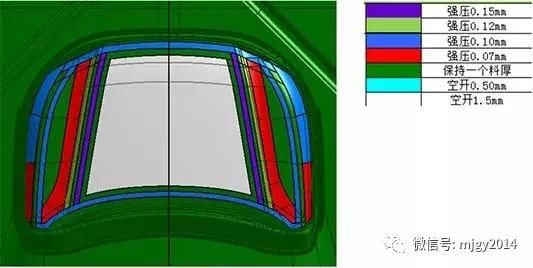
圖6 機(jī)蓋外板強(qiáng)壓工藝
但強(qiáng)壓工藝有一定的局限性,只考慮型面角度差帶來(lái)的間隙偏差,并沒(méi)有考慮板料在拉深過(guò)程中變薄而帶來(lái)的研合間隙偏差,且依靠經(jīng)驗(yàn)設(shè)置強(qiáng)壓值并不能解決所有零件的偏差,故該方法不能徹底消除間隙偏差導(dǎo)致的研合困難。
虛擬合模技術(shù)的應(yīng)用
4
現(xiàn)引入虛擬合模的概念,通過(guò)AutoForm軟件分析板料成形過(guò)程中各區(qū)域的變薄情況,模擬模具閉合過(guò)程,根據(jù)板料各區(qū)域的變薄量及角度差制定相應(yīng)的強(qiáng)壓工藝,替代依靠經(jīng)驗(yàn)設(shè)置強(qiáng)壓工藝,能更加精準(zhǔn)控制型面各區(qū)域的間隙。
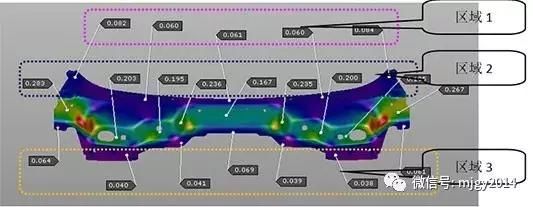
圖7 零件成形變薄量
以某汽車(chē)搭接件闡述虛擬合模的概念及應(yīng)用,第一步采用AutoForm分析板料在成形過(guò)程中的各區(qū)域變薄量t,如圖7所示,制件變薄梯度主要分3個(gè)區(qū)域,區(qū)域1板料變薄量約0.06mm、區(qū)域2側(cè)壁板料變薄量約0.16~0.28mm、區(qū)域3法蘭邊板料變薄量約0.04mm。
第二步以區(qū)域1的板料變薄量作為參考基準(zhǔn)值η,擬定在區(qū)域1對(duì)應(yīng)的上模零件型面進(jìn)行η=0.06mm的強(qiáng)壓補(bǔ)償,采用AutoForm軟件模擬上模閉合到底前0.06mm時(shí)各區(qū)域模具零件型面的間隙離空值h,用GOMinspect軟件將其呈現(xiàn),如圖8所示。
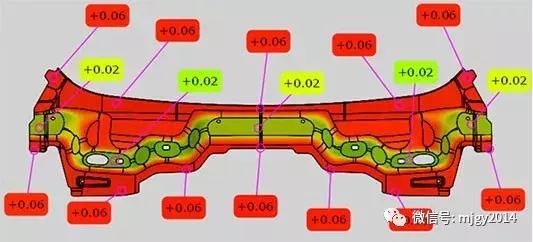
圖8 模擬上模到底前0.06 mm各區(qū)域模具型面間隙
上模到底前0.06mm時(shí),區(qū)域1與區(qū)域3的模具零件型面間隙離空值為0.06mm,由于角度差的存在,區(qū)域2側(cè)壁零件型面離空值為0.02mm。由此可知,在不考慮板料變薄時(shí),當(dāng)區(qū)域1與區(qū)域3進(jìn)行0.06mm的強(qiáng)壓時(shí),區(qū)域2側(cè)壁只需要進(jìn)行η-0.02mm=0.04mm的強(qiáng)壓即可滿足各區(qū)域制件同時(shí)接觸模具零件型面。當(dāng)考慮板料變薄因素時(shí),得出強(qiáng)壓設(shè)置公式θ=-t+η-h來(lái)滿足各區(qū)域型面的間隙要求。
區(qū)域1最終的強(qiáng)壓值:θ=-0.06+0.06-0.06=-0.06mm
區(qū)域2最終的強(qiáng)壓值:θ=-(0.16~0.28)+0.06-0.02=-(0.12~0.24)mm
區(qū)域3最終強(qiáng)壓值:θ=-0.04+0.06-0.06=-0.04mm
其中,θ為上模零件型面所需的強(qiáng)壓量;t為板料成形后的變薄量;h為在初始參考基準(zhǔn)值下上、下模零件型面的離空數(shù)值;負(fù)號(hào)表示強(qiáng)壓是向下模側(cè)置補(bǔ)償。
第三步通過(guò)UG或者CATIA軟件將各區(qū)域強(qiáng)壓量補(bǔ)償?shù)郊庸?shù)模,完成補(bǔ)償?shù)募庸?shù)模各區(qū)域型面的強(qiáng)壓值如圖9所示。
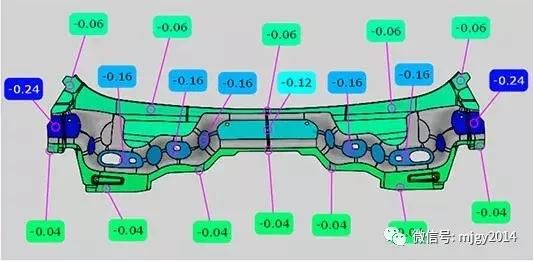
圖9 型面偏差加工強(qiáng)壓值
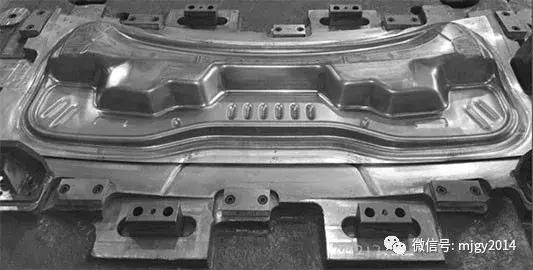
圖10 現(xiàn)場(chǎng)實(shí)際研合效果
該制件運(yùn)用虛擬合模技術(shù)后的研合效果如圖10所示,拉深模在研合8h后模具零件型面研合率已達(dá)到90%以上,成功縮短研合工時(shí),提高了研合效率。